IAPMO & Uniform Codes Change Meeting Emerging Technologies & Systems
The American National Standard Uniform Plumbing and Mechanical Codes undergo significant revisions every three years to incorporate new technologies and systems. This is done under an ANSI-designated consensus process that gives all stakeholders a voice and a vote in the final document. The process ensures a “balance of interest” that prohibits a single group from dominating the direction of code development and minimizes self-interest. A true consensus code development process offers transparency for all interested parties as well as the right of appeal. The model codes protect the health and safety of all users, and any changes made to them come as a result of thorough research and debate.
The newly released 2012 Uniform Plumbing Code aids the user with improved layout design features through the incorporation of our manual of style and innovative efficiency standards and sustainable practices. This edition includes significant changes with new provisions for alternative water sources for nonpotable applications, rainwater catchment systems, plumbing facilities and joining methods for water supply and drainage piping.
Chapter 4 has been significantly improved through reorganization in the area of plumbing fixtures by expanding use and application, water consumption and installation requirements. For example, a recommendation for approval as modified for showers that incorporated their application to applicable referenced standards includes water consumption requirements for a maximum flow rate in accordance with ASME A112.18.1/CSA B125.1. An added provision reduces the risk of scalding by requiring individual and tub-shower control valves to provide such protection based on the flow rate of the showerhead installed at point of use. The addition of required waste outlet sizing, referencing material and sizing provisions, and removal of the requirement for a finished dam curb or threshold to aid the aging population are among changes aimed at providing ease of use for the end-user.
Required plumbing fixtures is revised based on research conducted by ASPE, the Stevens Institute of Technology, American Restroom Association and School of Architecture with the Gender and Women’s studies program at the University of Illinois (Potty Parity in Perspective: Gender and Family Issues in Planning and Designing Public Restrooms). When designing satisfactory restroom facilities, factors that are considered to decide the minimum number of plumbing fixtures for a preferred service include occupancy, waiting times during peak demand, fixture use and likelihood of finding a vacant fixture. Potty parity does not always mean there will be the same number of toilets for women and men; parity is measured by the wait time to obtain a fixture. Where we see the most inconsistency occurring is in the number of required plumbing fixtures for women and men in mercantile and assembly occupancies that use the same ratio for both sexes. The 2012 UPC recognizes that women need more time, and the minimum required fixtures should accurately represent the population served based on design method.
Chapters 6 and 7 now offer various joining methods and connections to aid the end-user in identifying correct methods based on piping material.
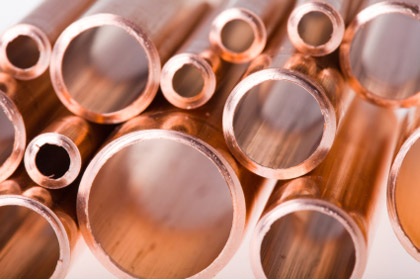
© iStockphoto.com/kotomiti
The material covered for water supply and water distribution joining methods includes: asbestos cement, brass, copper, CPVC, ductile-iron, PE, PE-AL-PE, PE-RT, PEX-AL-PEX, PP, PVC and stainless steel. The material covered for drain, waste and vent piping joining methods includes: ABS, asbestos-cement, cast-iron, co-extruded ABS, co-extruded PVC, copper, PE, PVC, stainless steel 304, stainless steel 316L and vitrified clay. Step-by-step guidance provides the user with clarification on acceptable methods of connection to piping materials.
Significant changes apply to Chapter 16 (“Alternate Water Sources for NonPotable Applications”) by expanding the scope with alternate water sources and developing code provisions that are specific to each one. The three areas addressed in Chapter 16 are gray water sources, reclaimed (recycled) water sources and on-site treated nonpotable water systems. The new water sources include three types of water disposal: subsurface irrigation, subsoil irrigation and mulch basin systems. Subsoil water irrigation provides a means to disperse shallow drip irrigation lines and mulch basins that collect and spread water in single- and multi-family dwelling applications. The reclaimed water provisions to on-site nonpotable water systems include gray water and other nonpotable water sources that are used for on-site applications. They are unique by installation through prepackaged or engineered systems that are listed and labeled for the intended application.
Chapter 17 is a new chapter dedicated to nonpotable rainwater catchment systems that includes input from the American Rainwater Catchment System Association. This chapter covers irrigation, toilet and urinal flushing with proper treatment; provisions where permits are required, maintenance of alternate water sources and minimum water quality.
Two new appendices cover potable rainwater catchment systems that include operation and maintenance requirements, minimum water quality, material compatibility, controls, backflow prevention, design and installation requirements and sustainable construction practices for plumbing systems as a resource for the Authority Having Jurisdiction.
The newly released 2012 Uniform Mechanical Code assists the end-user with enhanced layout design features through the incorporation of our manual of style and includes innovative efficiency standards and sustainable practices by allowing for a wide array of design alternatives to achieve minimum performance requirements in mechanical systems. In addition, the 2012 UMC underwent significant changes with new provisions for piping, tubing, balancing, louvers, ductwork, safety requirements for refrigeration machinery rooms and an alternative to calculate ventilation efficiency.
Significant improvements in Chapter 3 include provisions for a heating or cooling air system that provides specific requirements with return air, outside air or both, which are designed to replace required ventilation arranged to discharge into a conditioned space not less than the outside air specified in Chapter 4. Standards are referenced for louvers and their locations where installed in hurricane prone regions by providing minimum performance ratings for water rejection abilities and high-velocity wind conditions.
Provisions added in Chapter 4 offer an alternative for calculating ventilation efficiency through ASHRAE Standard 62.1 and updating minimum ventilation rates in breathing zones based on occupancy.
Safety requirements are updated and revised for refrigeration machinery rooms on vapor alarms, emergency control over the ventilation systems, control of ventilation systems and emergency controls.
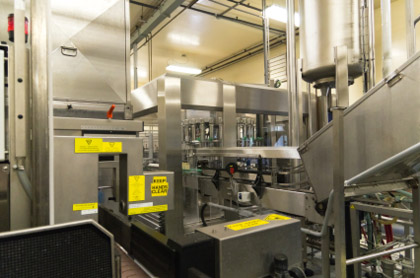
© iStockphoto.com/SimplyCreativePhotography
In addition, machinery room ventilation is addressed through the central control over the ventilation system and adding safety provisions for the emergency control through an identified switch. Detector location is critical to early leakage warning in refrigeration machinery rooms. Because machinery rooms are unattended most of the time, once the refrigerant gas is detected at the levels noted in Chapter 11, a local alarm must be initiated. The alarm is intended to alert occupants inside the area of detection and in the immediate vicinity to prevent any refrigerant gases that might escape from causing harm to those outside the area of release. In addition, the required detectors have the added important role of activating the emergency ventilation/exhaust systems in the machinery rooms.
The intent of this section is to provide a safe environment for emergency response personnel when responding to an incident in a refrigeration room. The emergency control switch is a tamper-resistant type that requires more than one action to actuate it. To prevent an accidental start-up, the switch must be capable of only stopping the controlled machinery, not restarting it. The switch must not affect the operation of such life-safety systems as detectors and exhaust equipment. In addition to the manual switch, the required refrigerant room detector must also shut down the same equipment when the vapor concentration exceeds the lesser of the detectors’ upper detection limit or 25 percent of the refrigerants’ lower explosive limit.
Refrigeration port protection in the form of a locking-type, tamper-resistant cap is added to address illegal venting of refrigerant service ports by unauthorized individuals. This inhalant sometimes poses a serious threat to human life and safety. The typical condensing unit is located outdoors and is equipped with access ports on the vapor and liquid refrigerant lines. These access ports allow for connection of diagnostic gauges so the refrigerant may be added to or taken from the unit during servicing. The purpose for this section is to prevent exposure to the refrigerant by illegal venting of refrigerant or intentional inhalation of refrigerant and refrigerant leaks that contribute to greenhouse gases in the atmosphere.
A new appendix provides a comprehensive set of technically sound provisions for sustainable practices and works toward enhancing design and construction of mechanical systems that result in a positive long-term environmental impact. Practices include water efficiency in systems through use of a submeter to monitor large water usage, including make-up water to cooling towers, evaporative condensers and boilers; establishing efficiency measures for cooling towers evaporative coolers; increased air quality provisions to reduce air contaminants and establishing minimum equipment efficiencies, system balancing, duct leakage, system sizing and systems controls, which add to the overall design and construction practices. A key feature is system commissioning that ensures such systems are designed, installed and maintained to function as intended over their life cycle, thus providing the most cost-effective strategy for reducing energy usage.
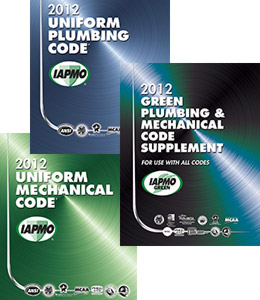
Images Courtesy of IAPMO
Members of the plumbing and mechanical industry are looking at these systems as part of the whole building as it relates to designers, owners, installers, operators, users and the community outside the building. Design options utilizing water reuse systems collect the water and reuse the water for irrigation, process water systems and flushing fixtures by using less water and energy. The future of plumbing and mechanical systems lies in the ability to design systems with the “whole building” in mind by using, preserving and respecting the natural biospheric earth systems of recycling air, waste and water. The 2012 UPC and UMC offer sustainable construction practices for both plumbing and mechanical systems, including up-to-date technical advances in the industry all in one document.